Two-thirds of electric vehicle (EV) battery fires happened when the vehicle was parked. That is 66% without any mechanical impact! In the first quarter of 2022, about 86 cases were disclosed to the media, of which 27.5% caught fire while charging and 38.5% while parked.1
Scary, but not surprising! Why?
Let me explain.
The role of battery management systems (BMS)
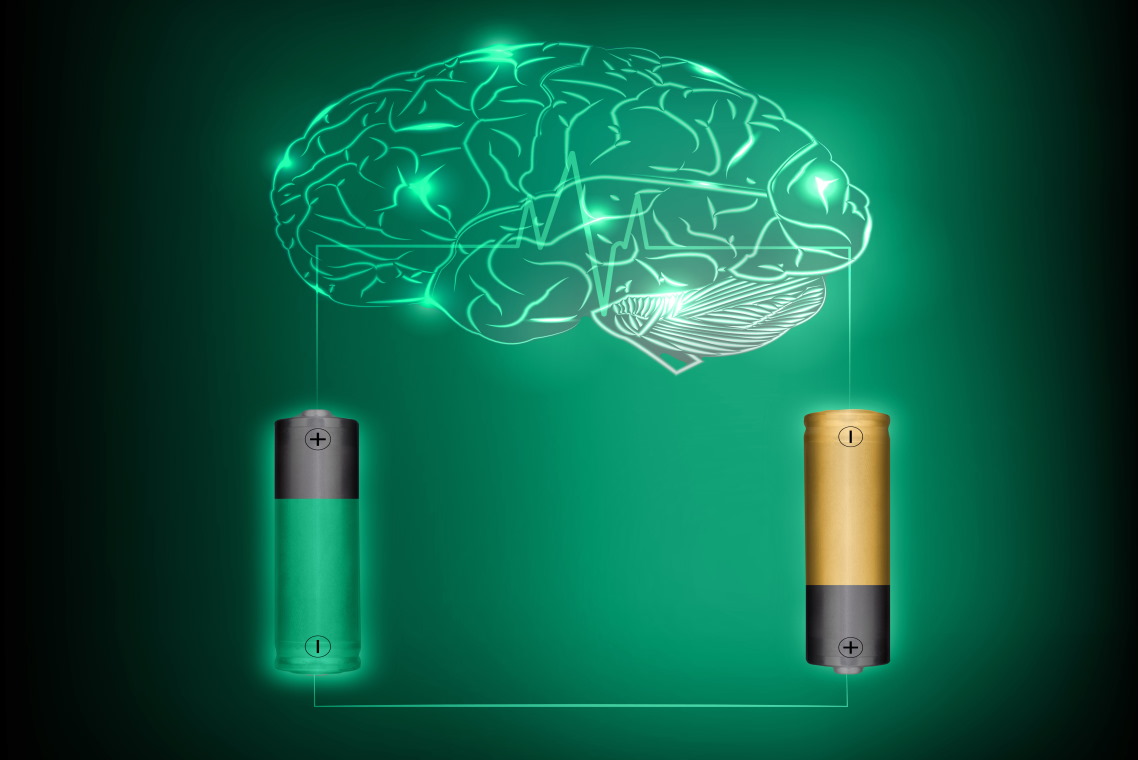
When a vehicle is charged, the battery should be safeguarded by the battery management system. But still, sometimes fires happen. How can that be?
To understand the role of battery management systems in battery safety, we need to understand what a BMS is. The battery management system is an integral part of all high-voltage battery systems. Think of it as the brain of any battery storage unit. It measures, monitors, controls, communicates and, most importantly, is responsible for safety through decision-making. The quality of these decisions has a direct impact on system safety.
So, the battery management system makes critical decisions to ensure system safety and deals with lots of data to do its job. Surely, that means the more data, the merrier, right? Not really. Throwing in additional sensors, additional algorithms, and complex systems logic might sound logical to make better decisions, but these can sometimes be counterproductive.
Lots of data does not equal better decisions
Decision-making should be a meticulous process of data handling and analyzing. Data needs to be acquired, stored, processed, sorted, and finally used as the base for decisions. To understand this, let us look at the following challenges:
- Analyzing data is a processor-intensive task. The more data you process, the longer it takes to find the decision-critical data and for the decision to happen. This leads to delayed and poor decisions.
- Data traffic and bandwidth in BMS channels are a real problem! Just like your PC might sometimes feel bottlenecked with your inputs and freezes to sort out the data, BMSs also encounter such freeze situations, leading to delayed and error-prone decision-making.
- High-volume data does not always translate to a better decision. Often, the design choice is to pack more sensors to get more data points, not considering qualitative factors. The design language should focus on a qualitative, rather than quantitative approach to acquire data.
- The BMS hardware design should be cohesive with the data environment. This defines how a good BMS design enables better decision-making overall.
If I were to choose, I would choose less but more strategically clever data. How much is too much is subjective to individual design, so there is no one-solution-fits-all. But, in simple words: too much data is sometimes worse than poor data!
Are all battery fires due to BMS mishaps?
Certainly not. It is fair to point out cell quality or go a step further and point out the chemistry or type of cell. But if the fire starts spontaneously while charging, it is usually the battery management system that needs to be addressed. Because regardless of the cell type (cylindrical, prismatic, pouch), if you keep pumping in current beyond a certain limit, you will hurt the cells. So, what is supposed to prevent this from happening? Usually, the BMS – in some cars, the Vehicle Control Unit (VCU) also has a part to play.
It is easier (mostly fair, too) to blame the cell. But the cell is just an “energy storage unit.” Think of it as a water tank and your current as water. If you keep filling the tank beyond the point of capacity, it is going to overflow. It is the job of the control unit—the brain—to monitor the water level, communicate with the water pump, and to stop pumping water into the tank if required. To do so, it must consistently and diligently measure the water level.
The role of battery management systems in battery fires
Sometimes batteries catch fire even when the battery is not charging. What role does the battery management system play in such cases? Cell balancing is one of the most underestimated aspects of lithium-ion battery pack designs.
Cell balancing done wrong can lead to thermal events. It might sound odd, because the most obvious causes are overloading during operations, bad thermal design, passive cooling, poor or slow BMS decision-making, etc. But cell balancing should not be overlooked to understand and prevent thermal runaway.
Why investigate cell balancing as a cause of thermal runaway
Cell balancing is a process whereby the cells are charged (or balanced) to the same level. Imagine two cups, one filled to the brim, the other filled to 95% of its capacity – how can we get these two cups to have the same percentage of capacity filled? Balancing! Let us have a closer look:
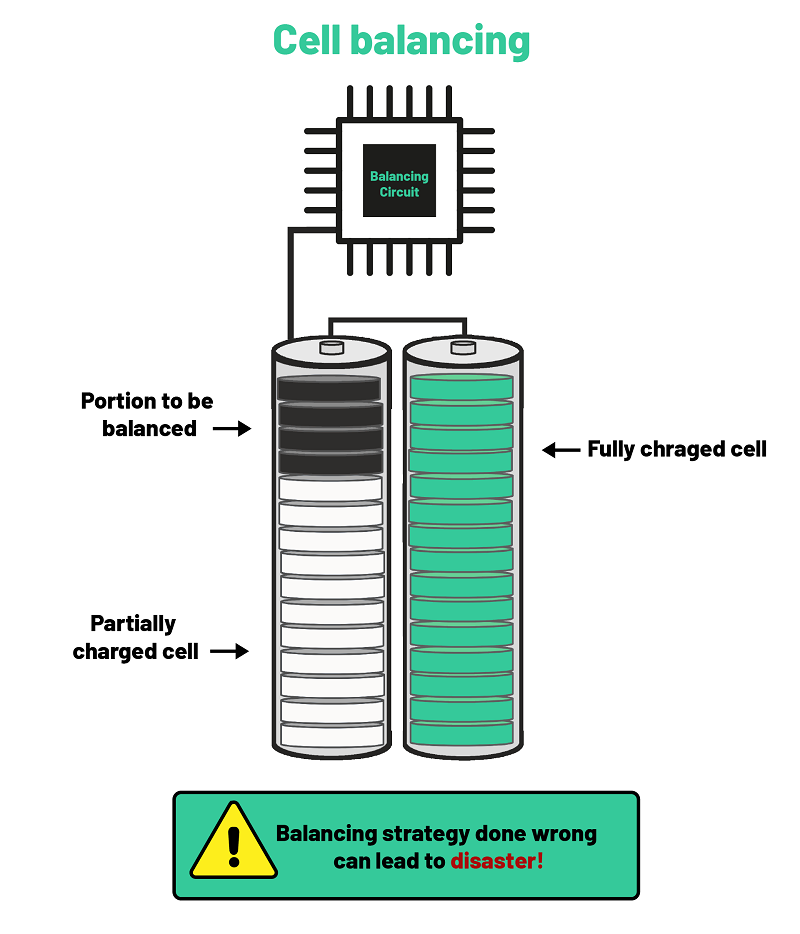
- Cell balancing can be executed in multiple ways: passive, active, or hybrid. All these balancing methods are monitored and controlled by the battery management system. Active balancing, as the name suggests, can actively pump in current. Passive balancing, the most used method, uses resistor-based balancing where the cell with excess charge will balance by ohmic losses. Hybrid uses both active balancing and passive resistors. Regardless of the balancing method, choosing the right balancing current is crucial.
- If the balancing mode (software, hardware selection, designing the balancing modes) is not meticulously designed and validated, this can lead to instances where the balancing mode pumps in too much current (overcurrent) or too little, leading to irregular aging.
- Usually, automotive implementations are safeguarded by ISO 26262 guidelines and audits. However, non-automotive applications are not necessarily governed by stringent regulations. Overlooking this quality-assurance step or cutting corners in testing can lead to thermal events during operation.
- Balancing is heavily dependent on the cells. Every cell has its SoC-OCV (state of charge – open circuit voltage) behaviors. So, taking an existing BMS and balancing circuit, and implementing them in a new cell is not going to work as intended.
- Balancing is done at rest. In some cases, between charging cycles. This means the battery is not being discharged. So, if the balancing does lead to an overcharging event that the BMS is not able to monitor quickly enough, it will be too late, leading to a thermal event.
I could author a small book on how not to design a balancing circuit. But to summarize, every circuitry design is unique due to the cell selection and BMS implementation strategy.
Learn more: How to Avoid Thermal Runaway
What factors affect BMS design?
Well, many. But, to simplify the story, let us start with these four:
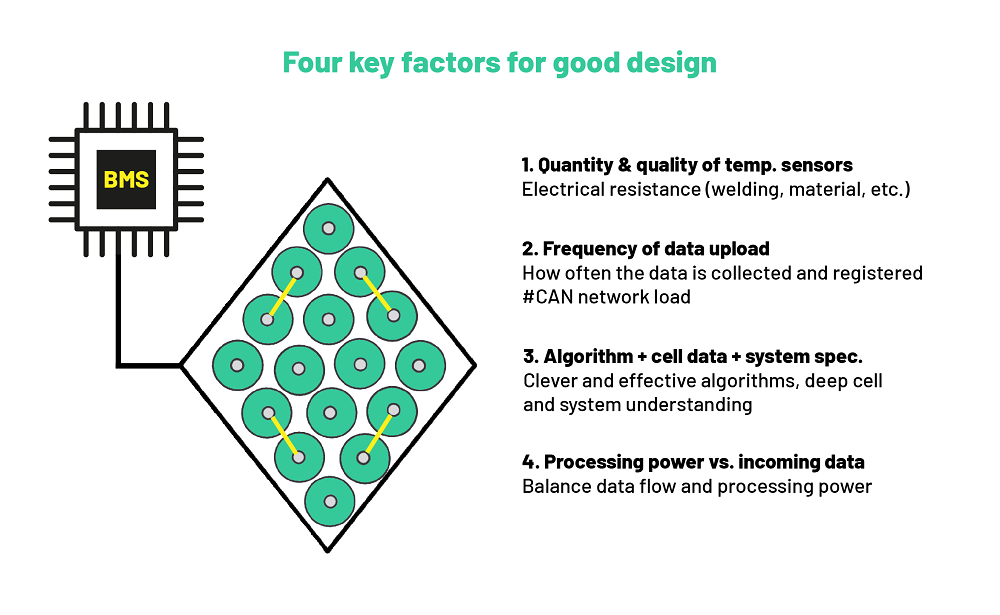
- Quantity and quality: Quantity and quality of the sensors which are used to monitor the cells. Several factors could affect such a decision. So, just listing component names will not get us far. Instead, key things to consider are inertia, tolerance, range, and sensitivities of the sensor itself.
- Frequency of data uploads: How often do I want to read out the values? The frequency determines the data volume. Deciding on data frequencies is system specific and needs careful consideration. For example, cell voltages are usually measured more often than system ground-fault detection.
- Algorithms + cell data + system specification: These are crucial. Deep understanding of the cell and the algorithms designed to handle the system specifications is essential. You could get away with poor or low-traffic data with clever algorithms, but the other way around is disastrous! Imagine a truckload of quality data the algorithm cannot make sense of in the given time. Recipe for failure!
- Balancing the processing speed with bandwidth: You could increase the processing power to handle data bandwidth (CAN traffic). But too much data is also not productive. The frequency and magnitude of data coupled with the nuance of the BMS processing power to pick up crucial data will have to be a balance between safety, ISO 26262, component availability, and maturity of the algorithm to identify culprits and react.
As “the brains” battery management design is crucial and plays a significant role in battery safety, particularly to stop overcharging and as part of cell balancing circuits. If the BMS is supposed to monitor battery safety, who is monitoring the BMS to ensure that it is doing its intended job? That is where cloud-based battery analytics come in, which I will cover in my next article.
Stay tuned and sign-up for the Battery Knowledge newsletter to get articles sent straight to your inbox!
1 https://batteriesnews.com/7-battery-electric-cars-day-catch-fire-china-most-involved-brands/
Article retrieved: September 26, 2022