Big Data is a widespread term across many industries, and it has also reached battery engineering. But what does Big Data mean and how is it relevant to lithium-ion batteries?
To understand what makes battery data “big” and how you can benefit from using it, it helps to look at the commonly used definition of Big Data through the five V’s: Volume, Variety, Velocity, Value and Veracity. Each of the V‘s highlights a particular aspect of Big Data and helps explain the challenges faced when handling Big Data.
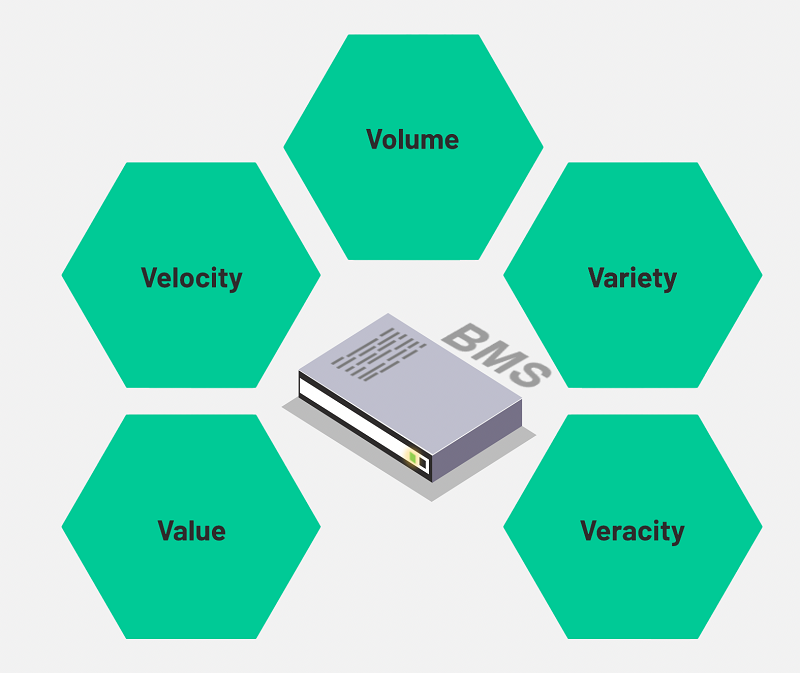
Volume: It starts with BMS data
Volume is the easiest V describing Big Data because it’s all about size. According to the definition of Big Data it starts from Terabytes (1 Terabyte or TB equals 1,000 Gigabytes) and goes all the way to Pettabytes. One Pettabyte (PB) equals 1,000 Terabytes.
In the battery space, data volume is generated by the battery management systems (BMS). The volume of data generated by a single BMS is small and doesn’t fit into the scope of Big Data. However, when we start collecting historic BMS data, we easily get into the Terabyte range of data volume. Depending on the application and the complexity of the battery system, a given system can have multiple sub-systems (modules in most cases) that send data to a central collection unit. For example, a PV home storage system can have 1 to 4 modules (5 kWh to 15 kWh) sending data, whereas a large, grid-scale battery storage unit can go all the way up to 6 to 6000 modules (50 kWh to 500 MWh) continuously sending data. So, in addition to collecting the data and storing the historical data, increasing system size and complexity can cause the data volume to add up fast.
Just storing this amount of data can pose a challenge for battery system owners and operators in addition to public transportation authorities with growing electric fleets. It’s important to consider the data pipeline for battery data whenever a new battery asset or electric vehicle (EV) is purchased and deployed. That is the tools and processes you will need to automate the movement and storage of the BMS data and the transformation of the data between the source system and your target database.
PRO TIP: A common solution is the use of cloud storage and computation, which allows for near-endless scalability.
Variety: The essence of Big Battery Data
Having a high volume of data is challenging enough but having Variety within that data increases complexity. What data is available and in what resolution depends heavily on the application the battery is used in. A home storage system might provide current, voltage, and the power delivered by the solar system. An electric bus would provide velocity, requested power, voltage, and current.
When it comes to resolution, the variety is also significant, going from resolutions of 1-5 minutes in home storage systems, to 1 second or below in EV applications, depending on the signal. The data produced by the BMS also depends on the module manufacturer and the module integration into the larger battery system.
Keeping this data variety in mind during the design phase of a data pipeline will reduce painful workarounds later when new types of battery systems are introduced. A helpful concept and technology to consider here is the data lake, a non-relational data storage solution. Non-relational storage offers greater flexibility than traditional relational databases by accommodating different data formats.
Velocity: As fast as the computational power can carry
The Velocity or speed factor and with it real or near real-time analytics is something that was traditionally handled on the battery management system itself. No one likes to wait for results, but many processes in lithium-ion battery systems require immediate computation. In particular, battery safety algorithms have become more computationally intensive, making cloud computation a necessary addition to embedded BMS algorithms in order to maintain velocity and prevent critical failures.
Handling high-velocity data in turn influences design decisions on the cloud backend, such as whether to go with batch processing or event-based data processing. Batch processing allows for scheduled computation of large datasets but is not always suitable for real or near real-time analytics. Event-based data processing is often a good option for time-sensitive analytics. It’s key to finding the right balance.
Value: Why bother with Big Battery Data?
Value is the underlying reason for tackling all other technical challenges Big Data brings with it. After all, having data is worthless if it cannot be used to generate value. Value is created in the battery industry by analyzing collected data to:
- Reduce safety risks and related costs
- Inform battery supply chain decisions
- Monitor warranties
- Extend battery lifetimes
Data analysis protects businesses from damages and unplanned downtimes while increasing the profitability and sustainability of battery assets.
This is where battery analytics come in to create value from Big Battery Data, for example by:
- Gaining transparency into the operational behavior of batteries and comparing it to manufacturer specifications. Answering questions such as, are you getting what you paid for, or are assets underperforming? Will your electric vehicles meet end-customer warranty conditions? And which suppliers’ batteries perform best under your given operating conditions and charging routines?
- Continuously monitoring safety to prevent critical failures and reduce operational risk.
- Using advanced machine learning-based aging models to confidently predict battery degradation, on which robust business plans can be made. Answering questions such as, will preventative maintenance to improve operating conditions generate greater returns?
Veracity: Quality in, quality out
Veracity encompasses the accuracy and validity of the data. Validity can be challenging due to the above-mentioned properties: volume and variety. An outlier voltage for one system might be the nominal voltage for another. Adding context to BMS data within the data pipeline, for example through metadata about the battery system, can help to assure the validity and provide essential boundary conditions for accuracy checks downstream.
Understanding that battery data fits into the paradigm of Big Data and then acting accordingly to develop data pipelines to handle the volume, variety, and velocity ensures that Big Battery Data can create value. It sets the necessary foundation for advanced battery analytics at scale, leading to deeper insights, better models and a higher understanding of each battery's state in operation.
What about lab test data?
If you want to better understand batteries, then analyzing their behavior in the real world is indispensable. Lab tests are important, but they are expensive, time-consuming, and have defined parameters. Battery management system data from the field is different. It shows the battery behavior under real-world operating conditions and is generated at no additional cost.
What’s more, battery analytics that leverage Big Battery Data have more information than lab tests and are more cost-effective. The number of tests needed to get a comparable amount of Big Battery Data isn’t timely or economical. Yet, big data (particularly volume and variety) is key to drawing a more accurate picture of your battery system and to detect anomalies.