Initially, lithium plating received little attention because early LIBs were primarily used in consumer electronics, where conditions rarely caused the problem. Now that LIBs are the motor on our path to sustainable transportation and finding more usage in electric vehicles (EVs) and larger grid applications, the conditions under which lithium-ion batteries must function safely and reliably are widening. In this article, I will explain why the conditions under which the batteries are used in electric vehicles can lead to lithium plating and examine the effects it has on the cells.
What You’ll Learn in This Guide:
- Key terms and their defintions
- Causes of lithium plating
- Effects of lithium plating
- The role of lithium plating in battery safety
- How to detect lithium plating
This article will introduce many new terms around lithium plating. Because not everyone is a battery expert, here’s a quick explanation of key terms to help you get started.
Lithium plating occurs when the electrochemical potential of the anode is equal to or lower than the potential of metallic lithium. This means the lithium ions that arrive at the anode cannot distinguish the anode material from metallic lithium and deposit in the metallic form instead of the desired intercalation into the anode.
Interestingly, in the widely used Nickel-Manganese-Cobalt (NMC) LIB type, the anode material is graphite which has a potential very close to elemental metallic lithium when it is saturated with lithium ions. This is the reason why lithium plating can occur on this material.
Lithium plating occurs under two main conditions during the charging process:
- Low temperatures
- High currents (fast charging)
These two conditions can easily occur when you consider where and the way in which electric vehicles operate and charge.
Lithium plating can also occur if the anode is overcharged. However, this usually doesn't happen unless there is a cell production error. Normally, the anode is oversized compared to the cathode to prevent overcharging.
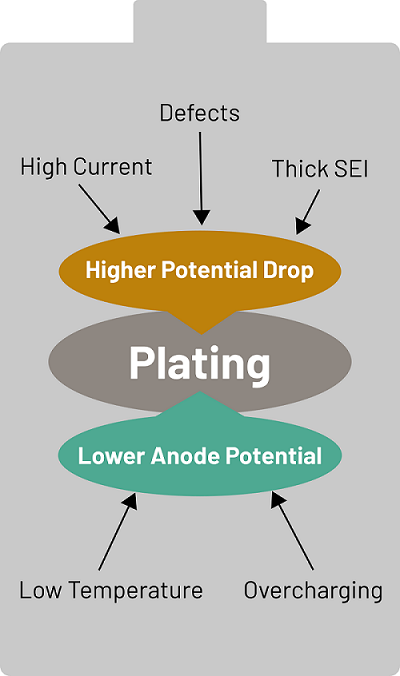
Lithium plating caused by charging at low temperatures
The ideal temperature for charging a lithium-ion battery is between between 5°C to 45°C (41°F to 113°F) and between 10°C and 30°C (50°F and 86°F). Below this range, ion diffusion within the anode slows significantly, causing lithium to build up on the surface. This buildup leads to a drop in the anode’s potential, causing metallic plating instead of proper intercalation.
EVs operating in cold climates often face this challenge. To prevent plating, batteries are sometimes pre-heated before charging, but this adds time and energy consumption.
Lithium plating caused by charging with high currents
Fast charging—one of EV owners’ most desired features—requires high currents. During fast charging, lithium ions quickly overload the anode surface, dropping its potential and inducing plating.
Plating under high current can also result from imperfections in the anode (e.g., cracks or contaminants created during cell production). Notably, lithium plating can occur even under moderate temperatures if the current is excessively high.
Watch the video: How lithium plating causes capacity loss and safety risks in lithium-ion batteries
The most common effects of lithium plating include:
- Reduced capacity
- Faster aging
- Increased internal resistance
Now, let’s dig into the details. Plating causes temporary metallic lithium deposits on the anode surface. Over time the deposits can be reused during a subsequent discharge or will diffuse into the anode again. All the lithium that is recovered this way is called reversible plating and has no further effect on the cell.
Depending on the severity and morphology of the plating, some plated lithium can react with the electrolyte or damage the anode surface. This is called irreversible lithium plating. Once it starts, it becomes self-reinforcing.
Under normal operation, the surface of the anode is covered by an insulating layer composed of degenerated electrolyte called the surface electrolyte interphase (SEI). This layer is formed in the early life of a battery and will keep growing slowly over time. The occurrence of plating can damage this layer and force a re-formation of the layer, consuming electrolyte and lithium. Due to the consumption of lithium during this unwanted reaction, plating reduces the amount of active lithium inventory in the cell, leading to a loss of capacity.
Additionally, metallic lithium can lose contact with the anode surface and be completely covered by insulating SEI, rendering it inert and leading to further capacity loss. Capacity loss caused by plating is much larger than the loss caused by normal battery cycling aging.
This newly formed SEI layer can also have a different morphology, being much thicker than the original layer and containing cavities that were created by the deposited metallic lithium. This inhibits ion flow through the SEI and increases the internal resistance of the cell. An increase in internal resistance reduces the battery's performance by reducing the maximum available power. In EVs, an increase in internal resistance would cause slower acceleration and longer charging time.
And that’s not all! The accumulation of lithium reaction products in the cell is also linked to the sudden death or knee point effect. Here the cell’s aging rate is suddenly and drastically increased, with the cell losing its remaining capacity within a few cycles. For the first life of the battery, the planned end of life of a cell is at around 70 – 80% remaining usable capacity; for second-life applications, a knee point effect can be detrimental.
Apart from the significant capacity loss and increased internal resistance, plating also compromises battery safety. Lithium ions will find the shortest way to deposit, so they prefer locations that already have plating. This can lead to a localized growth that will eventually result in what’s called a lithium dendrite on the anode surface. Dendrites look a little bit like narrow trees with sharp branches.
In the worst case, dendrites can pierce through the separator between the anode and cathode, causing a short circuit in the cell. Short circuits cause rapid cell self-discharge and can even lead to a thermal runaway.
.png)
If plating is detected during the charging process, it can be prevented. However, most current methods only detect plating after it has already occurred. Here’s how it works and the advancements being explored to identify plating more effectively.
Traditional Methods of Detecting Plating
One common detection method looks at the discharge curve for what's known as a “stripping plateau.” This plateau, visible in the cell voltage, happens because metallic lithium deposits on the anode surface, raising the discharge voltage.
Another approach is to observe the cell voltage during the relaxation phase right after a plating event. When plating occurs, the voltage initially shifts toward the metallic lithium potential on the surface. Over time, as some of the lithium diffuses back into the anode, it transitions back to the normal graphite anode potential.
Experimental techniques for detecting plating during charging are also available. These involve precise measurements of changes in the cell's temperature or thickness. However, they require costly external equipment and sophisticated battery management systems, making them impractical for many real-world applications.
Promising Techniques in Development
Research is underway to develop methods that could detect plating in real time by monitoring changes in the battery's internal resistance. These advancements could soon enable batteries to identify plating during charging automatically. If plating is detected, the system could warn the user or halt the charging process to prevent further damage.
Current Limitations in Real-World Applications
For most real-world scenarios, the signals commonly monitored in batteries include voltage, current, and temperature. However, there are limitations:
- Temperature is often measured at a system level instead of at each individual cell, making it difficult to detect plating in specific cells.
- Current is controlled and used to manage charging, but plating thresholds are highly dependent on temperature and vary between batteries.
- That leaves voltage as the most reliable indicator for identifying potential plating events during charging.
How Cloud-based Battery Analytics Help Detect Plating
With the use of battery safety analytics, continuous safety monitoring can recognize early signs of a failure and unsafe behavior that could be caused by lithium plating. ACCURE's cloud-based battery analytics solutions also have access to larger data sets that help in understanding the plating indicators and inform the development of new algorithms and the application of existing analytic methods to prevent plating before it can happen. Various use cases can provide different insights, helping make the methods more robust and reliable.
The more we know about batteries and their behavior in the real world, the better we can manage them to increase safety and reliability, and extend lifetimes.
Learn more about battery safety and types of battery faults in the Battery Safety White Paper.