Batteries are at the heart of our energy and mobility future. But with the ever-increasing numbers of deployed battery packs around the world, we also see more incidents of failing systems – from burning electric scooters in apartment buildings in New York City to a series of electric bus fires in Paris and London. So, what are our options to prevent critical failures and make batteries—and clean energy—as safe as possible?
Faults and financials
The financial risks associated with faulty electric vehicle (EV) batteries can be derived from two major recalls that happened after a series of battery fires in 2020 and 2021. In both cases, batteries from LG went into thermal runaway during orafter charging:
The US$900 million Hyundai Kona case
(at least 15 incidents)
Hyundai first tried to fix the battery issue with a software update for the battery management system. When an updated Kona EV caught fire in January 2021, Hyundai issued a general recall of all its 76,000 Kona electric vehicles and 6,000 IONIQ models and electric buses that use battery cells made by LG Chem. The recall ended up costing Hyundai US$900 million.
The US$1.9 billion Chevrolet Bolt case
(at least 17 incidents)
General Motors (GM) tried two iterations of software updates but was unable to prevent more battery fires, among others in Virginia and Vermont, U.S. After that, GM told customers to park their EVs outside and not charge them unattended, before finally issuing a formal recall a week later. The recall became the most expensive recall ever on a per-vehicle basis and eventually led LG to compensate GM over US$1.9 billion.
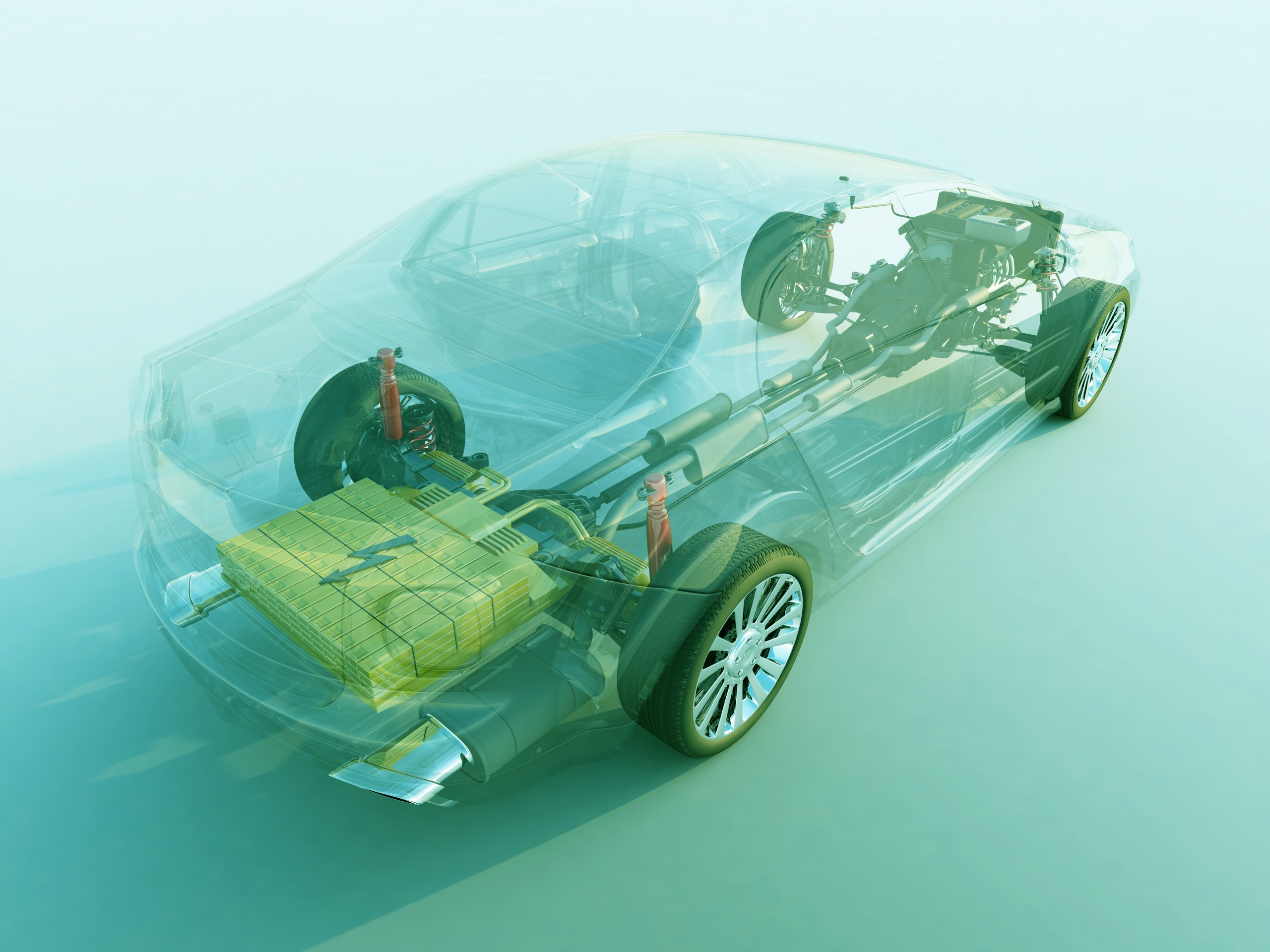
The route to safer batteries
So, what are the options to make batteries safer and to reduce financial risk? Generally speaking, there are three main areas:
1. Production quality
2. System design
3. Battery analytics
1. Production quality
To operate safely, batteries need to be produced with the utmost care and precision, from processing active materials to manufacturing the cells to assembling the pack. Any production defect can lead to unexpected (and sometimes critical) behavior years later.
The only solution to control manufacturing defects is rigorous quality management from incoming goods control to end of line testing. But there are two major challenges: for one,most mid-stream companies in the EV space have neither the full information about, nor the ability to impact the quality of the cells and packs they buy. On the contrary, in today’s market, the sheer ability to buy batteries from a supplier weighs heavier than any quality management (QM) certification. On top of that, even the most rigorous quality management will never catch 100% of the failures.
2. System design
Battery systems are equipped with several layers of protection meant to keep the battery in its intended window of operation, shield it from external harm, and minimize the impact of asingle-cell failure.
Passive safety components: From sturdy packaging to withstand crashes to hermetic sealing against water inflow, these passive safety components are last resorts to minimize the damage from critical situations that are already happening. They generally cannot prevent safety incidents.
Battery management system (BMS): BMSs are the brain of every Lithium-ion battery (LIB) system. They make sure a cell is not over or undercharged and they bring basic state estimation functionalities with them, including state of charge (SOC) and state of health (SOH). However, BMSs also have noticeable shortcomings: they only see the cells within the corresponding battery pack, have little to no access to historic data or data from other battery systems, and they have limited computing power.
The limitation of BMS safety algorithms was highly visible in the attempts of Hyundai and GM to solve their safety problems with a firmware update (in other words a BMS software update). While it’s possible to locally scan the sensor data for anomalies, such as rapidly changing impedances or sudden voltage drops, as precursors for thermal events, the lack of baseline data and ongoing comparisons to similar systems strongly limits the value of such analyses.
3. Cloud-based battery analytics
A proven strategy to prevent critical failures and improve battery safety is the use of cloud-based analytics. By detecting critical faults at an early stage using more sophisticated and modern analytical methods than available in any battery management system, automobile manufacturers and electric car owners can act before any damage is done. Diagnostics based on existing field data streams can be applied to any LIB system without the need for any product modification.